Catalog
Tags
Can a Boring Bar Function as a Drill? Exploring Alternative Holemaking Techniques
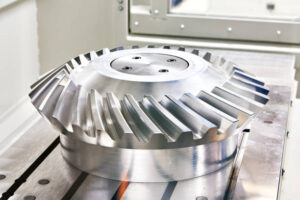
In machining, efficiency and tool versatility are key to maximizing productivity. A common question among machinists is whether a boring bar can double as a drill, especially when working with limited tooling or tight tolerances. While standard boring bars lack the proper clearance for drilling, some workarounds exist—such as using insert drills or specialized multi-tools like those from Iscar. However, these methods come with trade-offs in speed, chip evacuation, and tool longevity. This article explores the feasibility, risks, and best practices for using boring bars in unconventional drilling applications, along with alternative solutions for holemaking when dedicated drills aren’t available.
The Limitations of Boring Bars for Drilling
Boring bars are designed for internal diameter enlargement, not for plunging into solid material. Their geometry lacks the necessary clearance angles and chip evacuation paths required for efficient drilling. Attempting to use one as a drill often results in:
- Excessive tool pressure due to full insert contact during plunging.
- Poor chip clearance, leading to heat buildup and potential insert damage.
- Chatter and deflection, especially with smaller-diameter bars.
While some machinists report success with low feed rates (e.g., 0.001 IPR) in softer materials like aluminum or plastic, the process is significantly slower than conventional drilling and risks tool breakage in harder metals.
Workarounds and Practical Solutions
When a dedicated drill isn’t available, several techniques can mitigate the challenges of using a boring bar for holemaking:
- Pilot holes: Drilling a small starter hole (even with a spot drill) reduces the load on the boring bar during plunging.
- Peck cycles: Using G75 grooving or G72 canned cycles with minimal Z-depth increments (e.g., 0.003″ per pass) minimizes tool stress.
- Hybrid tools: Multi-functional tools like Iscar’s DRG-MF or EcoCut bars combine drilling, boring, and turning capabilities in a single toolholder.
For one-off jobs, modifying a twist drill to stub length or using an end mill to rough the hole may be more efficient than forcing a boring bar into an unsuitable role.
Specialized Alternatives for Deep or Precise Holes
For applications requiring deeper holes or superior finish, alternative tooling should be considered:
- Gun drills: Their rigid design and replaceable inserts excel in deep-hole drilling while leaving room for subsequent boring.
- Indexable insert drills: Tools like the Iscar DRG-MF offer better chip evacuation and higher feed rates than boring bars.
- High-feed milling: For flat-bottom holes, plunging with a center-cutting end mill before boring can save time and tool wear.
Investing in the right tooling—or advocating for it with management—often proves more cost-effective than compromising with improvised methods.
Conclusion: Balancing Creativity and Best Practices
While it’s technically possible to use a boring bar as a drill in certain scenarios, the practice is far from ideal. Success depends on material softness, hole depth, and careful parameter adjustments (e.g., ultra-low feed rates). For occasional one-off parts, techniques like pilot holes or peck boring may suffice, but for production work, dedicated drills or multi-functional tools like Iscar’s DRG-MF deliver better results. Machinists should weigh the time and risk of improvisation against the long-term benefits of proper tooling. When in doubt, consulting tool manufacturers or investing in versatile solutions ensures efficiency, precision, and tool longevity.
🌏 Looking for Reliable CNC Machining Services from China? We’ve Got You Covered.
At Ruixin Mold, we provide high-precision CNC machining services trusted by global clients across the automotive, tooling, and manufacturing industries.
Based in China with international standards, we offer:
⚙️ Tight-tolerance machining for complex parts
🚚 Fast turnaround times for both prototypes and production
🔩 One-stop solutions including heat treatment, surface finishing, and assembly
🛠️ Custom components like mold inserts, sliders, lifters, and ejector plates
We combine advanced equipment, experienced technicians, and a strong quality control system to ensure you receive exactly what you need — on time and on spec.
📦 Serving customers in Europe, the U.S., and Southeast Asia with stable, cost-effective manufacturing support.
📩 Need a CNC machining partner in China you can rely on? Let’s connect and talk about your next project!
Need Precision CNC Machining for Your Mold Components?
We specialize in custom CNC machining of mold inserts, slide cores, ejector plates, mold bases, and lifters
all made to your exact drawings and specifications.
👉 Let’s Build Your Next Project Together!
Tell us your needs and upload your drawings — we’ll get back within 24 hours.